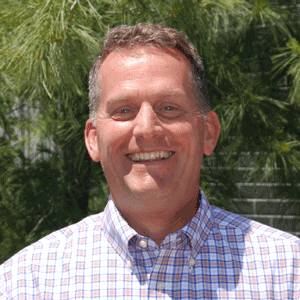
Charlie Mantione EVP PanurgyOEM
It’s time to upgrade your hardware…. or is it?
by Charlie Mantione
Every investment your company makes in technology comes with “Obsolescence Risk” which essentially begs the question;
Will new technology remain superior long enough for the investment to pay off, or will it become obsolete so soon that the company loses money?
Your well meaning vendor presents his upgrade proposal labeled as “2016 Technology Plan” or “Technology process improvement plan” or “2016 OpEx reduction plan” (translation: spend CapEx on new hardware and we’ll reduce your OpEx by discounting maintenance renewals)
I get it, the vendor has new models which they need to sell. They’ll seek out new customers but most technology vendors will go right down their current customer list to present proposals designed to influence customers to dump that nasty old hardware (which by the way was the greatest technology ever created 3 years ago) in favor of new models.
Why does equipment become obsolete? Three of the main reasons are:
Functional obsolescence: New features or functionality are available in new products which are required (or desired) to meet particular business goals or possibly the components only have a functional life of X years before wearing out.
Benefit to customer: New products or models may offer improved functionality that may map to a new business requirement or deliver more operational efficiency.
Financial obsolescence: A new version or model is more efficient and cheaper to run.
Benefit to customer: A newer, more efficient model could save money in the long run by either reducing labor costs, energy costs or by improving a key process.
Product End of Life: The manufacturer announces “end of life” and no longer covers product under warranty or your service provider (dealer) no longer offers maintenance agreements for product forcing a migration or upgrade.
Benefit to the customer: Business continuity may be assured by upgrading to new equipment reestablishing the factory or vendor backed warranties or maintenance agreements.
Sometimes it just makes sense to upgrade your equipment, but not always.
Does a manufacturer’s “end of life” always equal the product’s functional end of life
Vendors force obsolescence to suit their own interests, but what about your company’s interest? With the increasing speed of forced obsolescence, what’s the alternative to protect your investment without having to retire your equipment before it’s served its purpose (or paid for itself)?
Say you have a percentage of older equipment in your portfolio that just works. Maybe they’re older and may not be what you’d call “mission critical” but they print ID badges or signage or do something – do you really have to upgrade just because the vendor no longer offers support?
There are business models that can extend useful life for your investment.
PanurgyOEM, an electronic integration services company located in Rockaway, NJ, has process in place to help you design an alternate support plan to help you preserve your “obsolete” equipment. PanurgyOEM’s 30 years of experience and in-house expertise has helped hundreds of companies maintain their equipment in optimal fashion – all with more efficiency and often at a lower cost.
To see how you can develop a workable solution to maintain your not-so-obsolete equipment, contact us at 973-625-4056
Charlie Mantione is the EVP & Chief Revenue Office at PanurgyOEM. Charlie’s always looking for new partnerships and companies he can help extend the useful life of their hardware. He can be reached at 973-625-4056 or on LinkeIn: https://www.linkedin.com/in/charlie-mantione