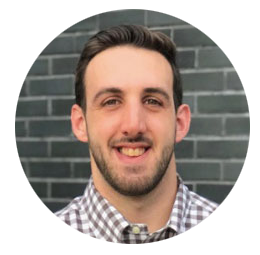
by Mark Palumbo
Director of Business Development, PanurgyOEM
Reverse logistics for electronics manufacturers, particularly those handling repairs in-house, can create a big problem for a departmental budget due to the inevitable variability in costs.
In this blog post, we’re going to dig into the top 10 reasons why the money electronics manufacturers spend on repairs and refurbishments can swing wildly. It could be anything from supply chain issues, to the complexity of the repairs, all mixing together to make your reverse logistics expense fluctuate.
Given our 40+ years in reverse logistics, we’re going to highlight the big issues that make costs vary so much. Identifying these factors can help you focus on strategies to better manage and reduce costs.
Here are the top 10 factors contributing to reverse logistics cost variability for electronics manufacturers:
1. Component availability: The cost of repair or refurbishment can vary depending on the availability and cost of the components required for the repair.
If certain components are in high demand or face supply chain disruptions, their prices may increase, leading to higher repair costs.
2. Seasonal demand: The demand for certain electronic products may vary throughout the year. If the returns department experiences higher volumes during peak seasons, the cost of repair or refurbishment may increase due to increased labor, equipment, and resource requirements.
3. Technological advancements: The rapid pace of technological advancements can affect the cost of repairing or refurbishing products. As newer and more complex technologies emerge, repairing older products may become more expensive due to the need for specialized knowledge, equipment, or components.
4. Warranty status: The warranty status of returned products can impact the cost of repair or refurbishment. If a returned product is still under warranty, the manufacturer may bear the cost of repair. However, if the warranty has expired or is void, the repair costs may be passed on to the customer or the department, leading to variation in overall costs.
5. Product lifecycle stage: The stage of the product’s lifecycle can influence repair costs. In the early stages, when a product is newly introduced, repair costs may be higher due to limited availability of spare parts or technical expertise. As the product matures and becomes more widespread, the availability of parts and repair knowledge improves, potentially reducing costs.
6. Regulatory compliance: Changes in environmental regulations or recycling standards can impact the cost of handling returned products. If new regulations require additional testing, certifications, or environmentally friendly disposal methods, the cost of repair or refurbishment may increase.
7. Economic factors: General economic conditions can affect the cost of repair or refurbishment. During periods of economic downturn, manufacturers may face cost pressures and attempt to reduce repair costs to maintain profitability. Conversely, during economic booms, manufacturers may invest more in repair capabilities, leading to higher costs.
8. Quality of returns: The quality and condition of the returned products can impact repair costs. If the majority of returned products require minimal repairs or have minor issues, the overall cost of repair or refurbishment may be lower. However, if a significant portion of returns are heavily damaged or require extensive troubleshooting, the costs can increase.
9. Repair complexity: The complexity of the products being repaired or refurbished can affect costs. More complex electronics with intricate designs, integrated components, or specialized features may require additional time, expertise, or resources, leading to higher repair costs.
10. External partnerships: The cost of repair or refurbishment can also be influenced by the relationships and partnerships the manufacturer has with external service providers or recyclers. The terms of these partnerships, including pricing agreements and service level agreements, can vary over time, impacting the overall cost of reverse logistics operations.
Managing reverse logistics in the electronics sector is a significant challenge. The interplay of diverse factors from component scarcity to regulatory compliance creates an ongoing challenge, impacting costs across the board. It’s clear that staying ahead in this always changing process requires not just insight but proactive action. This is where we come in.
Are you ready to optimize your reverse logistics operations and reduce the variable cost merry-go-round? We are here to help! Contact us today to schedule a strategy session.
Our team is equipped with the knowledge and tools to tailor a solution that not only addresses your current pain points but also positions you for future success. Don’t let the complexity of reverse logistics keep you from moving forward. Let us guide you through it. Schedule your strategy session now and take the first step towards efficient, cost-effective reverse logistics management.